contacto@xindustra.com
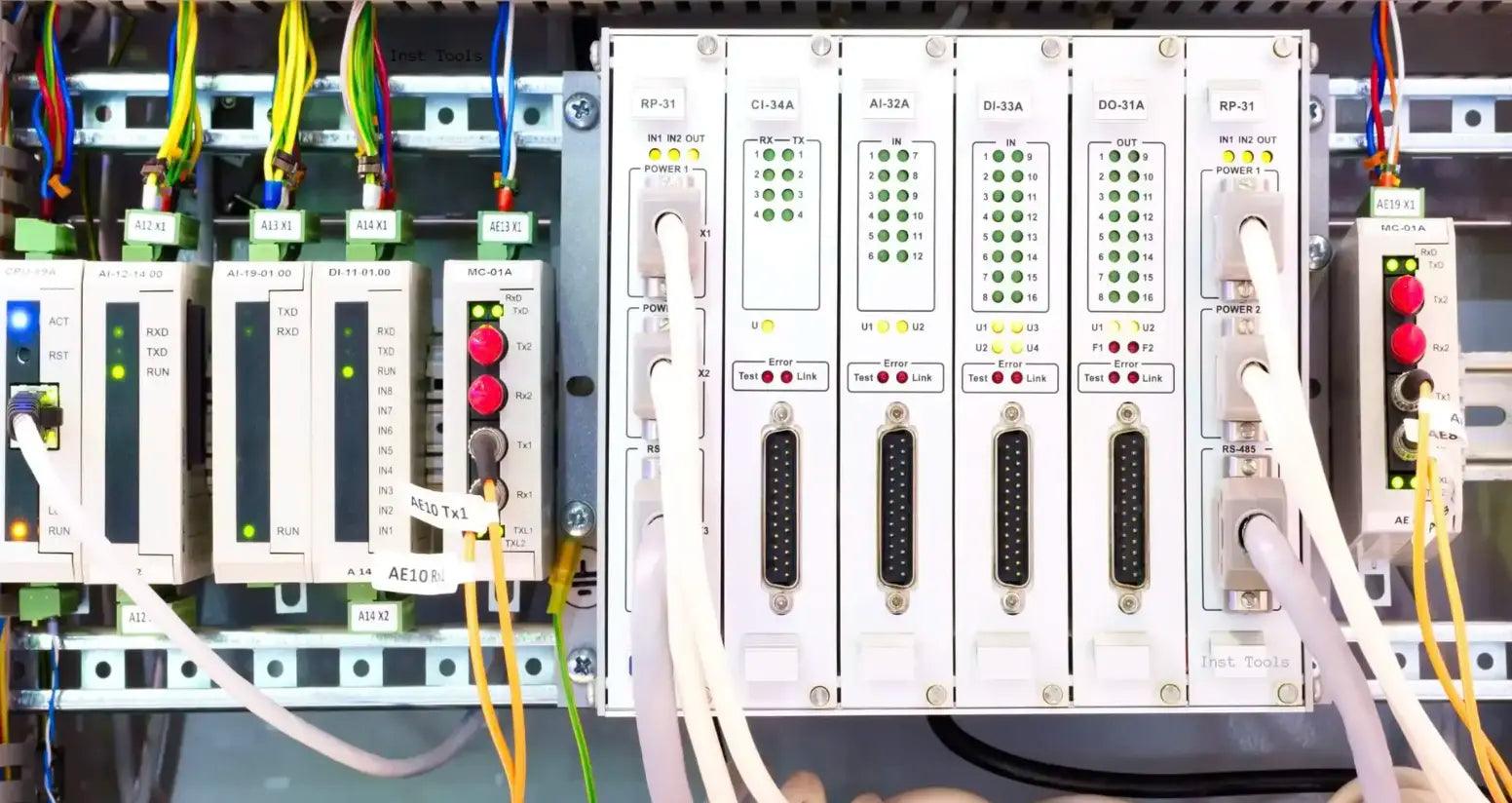
Comprensión de los protocolos de comunicación PLC más populares
La comunicación es una característica que puede estudiarse no solo en humanos y animales, sino también en máquinas. Al igual que las personas que nos rodean, las máquinas, en concreto los equipos de automatización, se comunican entre sí para transmitir información vital. Esta información se envía a equipos como brazos robóticos para ensamblar piezas de un producto o a PLC para indicar que una cinta transportadora se ha detenido. Esta comunicación se realiza íntegramente en un nuevo lenguaje desarrollado específicamente para el entorno industrial: los protocolos de comunicación PLC.
Estos protocolos constituyen la base de la automatización industrial, permitiendo que diversos dispositivos se entiendan entre sí y colaboren fluidamente. Regulan cómo se formatean, transmiten e interpretan los datos en las redes, garantizando que cada mensaje enviado se reciba y procese con precisión. Sin estos protocolos, la precisa secuencia de movimientos y acciones que damos por sentada en los sistemas automatizados sería imposible.
Los protocolos de comunicación PLC varían ampliamente en diseño, capacidades y aplicaciones. Algunos están diseñados para tareas sencillas y directas, mientras que otros están diseñados para tareas complejas de intercambio de datos y control en sistemas extensos e interconectados. Independientemente de su complejidad, el objetivo sigue siendo facilitar una comunicación fiable, eficiente y en tiempo real entre máquinas.
Lo esencial de los protocolos de comunicación del PLC
La clave de cualquier sistema automatizado reside en la capacidad de compartir información con rapidez y precisión. Aquí es donde entran en juego los protocolos de comunicación PLC, que actúan como lenguajes estandarizados que permiten la comunicación entre los dispositivos de estos sistemas. Pero ¿qué son exactamente estos protocolos y cómo funcionan? Analicemos sus conceptos básicos.
Comprensión de los protocolos de comunicación
Un protocolo de comunicación PLC es un conjunto de reglas que rigen la transmisión y recepción de datos entre dispositivos en un entorno de automatización industrial. Imagínelo como la gramática y el vocabulario que las máquinas usan para entenderse entre sí. Al igual que los humanos usan el lenguaje para transmitir ideas, las máquinas usan estos protocolos para enviar comandos, recibir actualizaciones de estado y coordinar acciones con precisión.
Cada protocolo tiene su propio "dialecto" o conjunto de reglas que definen todo, desde el formato de los datos y la velocidad de comunicación hasta la gestión de errores y la seguridad de los datos. Estos protocolos garantizan que un comando enviado desde una parte del sistema sea interpretado y ejecutado correctamente por otra, independientemente del fabricante o la tecnología específica utilizada.
El papel de los protocolos en la automatización industrial
La función principal de los protocolos de comunicación PLC es facilitar la interoperabilidad entre diversos dispositivos y sistemas en un entorno industrial. Esto incluye desde sensores y actuadores hasta equipos más complejos como brazos robóticos e interfaces hombre-máquina (HMI). Al adherirse a un conjunto común de estándares de comunicación, estos elementos dispares pueden funcionar conjuntamente a la perfección, mejorando la eficiencia, la fiabilidad y la flexibilidad de los sistemas automatizados.
Por ejemplo, en una línea de fabricación, un sensor podría detectar que un producto ha alcanzado una etapa específica del proceso de ensamblaje y comunicar esta información mediante un PLC a un brazo robótico. El brazo, al comprender el mensaje mediante el protocolo compartido, sabe entonces que debe recoger el producto y trasladarlo a la siguiente estación. Este nivel de coordinación es crucial para mantener la velocidad y la precisión requeridas en las operaciones industriales modernas.
Componentes clave de los protocolos de comunicación
Si bien los distintos protocolos difieren en sus detalles, la mayoría comparte algunos componentes clave:
- Codificación de datos: Cómo se convierte la información a un formato adecuado para su transmisión.
- Enmarcado del mensaje: La estructura de un mensaje, incluidos marcadores de inicio y finalización, datos y potencialmente información de verificación de errores.
- Medio de transmisión: Las vías físicas o inalámbricas a través de las cuales se envían los datos (por ejemplo, cables Ethernet, Wi-Fi).
- Sincronización: Mecanismos que garantizan que el emisor y el receptor estén alineados en el tiempo, lo que permite una interpretación precisa de los datos.
- Detección y corrección de errores: Métodos para identificar y corregir errores que puedan ocurrir durante la transmisión, garantizando la integridad de los datos.
Comprender estos componentes ayuda a comprender cómo los protocolos de comunicación del PLC gestionan la compleja tarea de interacción de máquina a máquina, sentando las bases para explorar protocolos específicos y sus características únicas.
Modbus
Desarrollado en 1979 por Modicon (ahora Schneider Electric) para sus PLC, Modbus se ha convertido en un protocolo de comunicación ampliamente adoptado. Su longevidad y ubicuidad son resultado directo de su diseño de protocolo simple y abierto, que permite una fácil implementación e integración en una amplia gama de dispositivos y fabricantes.
En esencia, Modbus permite el intercambio de información entre dispositivos en un entorno industrial, como entre un PLC (controlador lógico programable) y diversos sensores, actuadores u otros PLC. Es como tener un grupo de trabajadores en una fábrica, cada uno hablando un idioma diferente, pero necesitando coordinarse para completar las tareas eficientemente. Modbus sería el lenguaje acordado que todos deciden usar para comunicarse eficazmente.
Cómo funciona Modbus
Modbus se basa fundamentalmente en una arquitectura maestro-esclavo, donde un dispositivo principal inicia transacciones (consultas) para controlar o recopilar datos de dispositivos secundarios. Este diseño facilita una comunicación clara y dirigida dentro de las redes, lo que reduce la posibilidad de colisiones de datos y simplifica la resolución de problemas.
- Modbus RTU y Modbus TCP/IP : Modbus opera sobre dos medios principales: serial (Modbus RTU) y Ethernet (Modbus TCP/IP). Modbus RTU es reconocido por su simplicidad y eficacia en la comunicación serial, utilizando RS-232, RS-422 o RS-485. Modbus TCP/IP, por otro lado, extiende Modbus sobre redes TCP/IP, lo que permite la integración con infraestructuras de red modernas y aplicaciones del Internet de las Cosas (IoT).
-
Modelo de datos : Modbus define un modelo de datos simple que incluye entradas discretas, bobinas, registros de entrada y registros de retención, lo que permite transmitir una variedad de tipos de datos, incluidos valores binarios, resultados discretos y analógicos.
Imagine una línea de fabricación donde se llenan, tapan y etiquetan botellas. El PLC es el cerebro de la operación y se encarga de coordinar cada paso. Así es como Modbus podría entrar en juego:
- Detección de la botella : Al inicio de la línea, un sensor detecta cuándo hay una botella lista para llenarse. Este sensor se comunica vía Modbus para informar al PLC de la presencia de una botella.
- Llenado de la botella : Al recibir la señal, el PLC envía un comando Modbus a la máquina llenadora para que comience a llenar la botella. Tras completar la tarea, la máquina envía un mensaje al PLC indicando que la botella se ha llenado.
- Taponado y etiquetado : De igual forma, el PLC ordena a la máquina taponadora que tape la botella y a la etiquetadora que la etiquete, enviando y recibiendo cada vez mensajes vía Modbus para coordinar estas acciones.
Este proceso se basa en Modbus para facilitar la comunicación entre el PLC y las distintas máquinas. Sin él, no habría una forma estandarizada para que estos dispositivos compartieran actualizaciones de estado o recibieran instrucciones, lo que generaba ineficiencia y errores.